Introduction
W
hat is an EV Battery Management System? A Comprehensive Guide
Ever wondered what keeps your electric vehicle’s battery running smoothly? Well, buckle up because we’re about to take a deep dive into the world of EV Battery Management Systems (BMS)! This unsung hero of electric vehicles plays a crucial role in keeping your car on the road and your battery in tip-top shape. So, let’s pop the hood and explore the ins and outs of this fascinating technology.
EV Battery Management System Overview
The battery management system (BMS) is an electronic device composed of battery electronic components and a battery control unit. It can control the battery input and output power, monitor the battery status (temperature, voltage, state of charge), and provide a communication interface for the battery.
The battery management system is mainly used to improve the utilization rate of the battery, prevent the battery from overcharging and over-discharging, extend the battery life, and monitor the battery status. The electric vehicle battery management system is mainly used for real-time monitoring of the power battery parameters of electric vehicles, fault diagnosis, SOC value estimation, driving range estimation, short circuit protection, leakage monitoring, display alarm, charging and discharging mode selection, etc., and exchange information with the vehicle controller or charger through the CAN bus to ensure the efficient, reliable and safe operation of electric vehicles and ensure the safety of the vehicle during use.
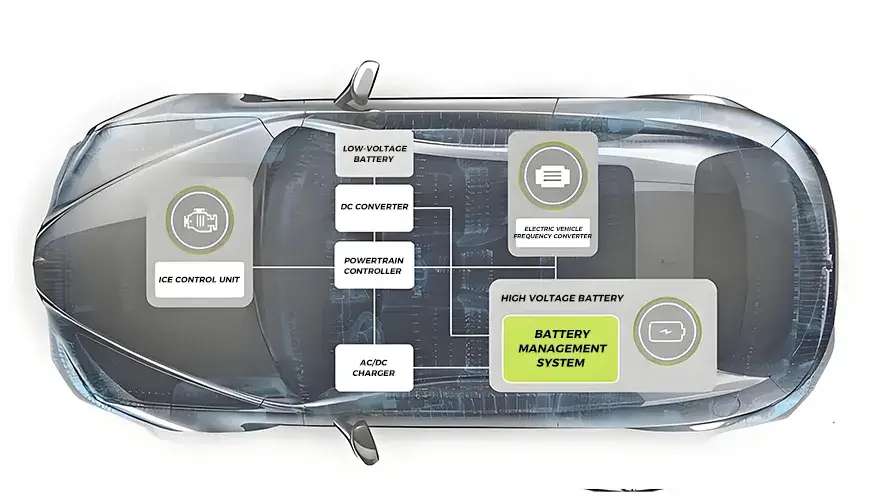
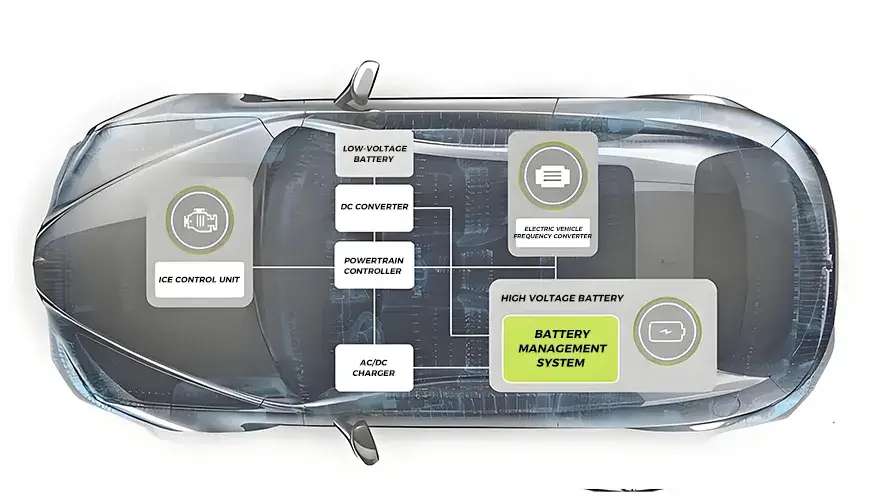
Main Functions of a Typical EV Battery Management System
1. Real-time collection of battery system operating status parameters: Real-time collection of the terminal voltage and temperature, charge and discharge current, and total voltage of the battery pack of each battery in the electric vehicle battery pack. Since the performance and status of each battery in the battery pack are inconsistent during use, the voltage, current, and temperature data of each battery must be monitored.
2. Determine the SOC value of the battery: Accurately estimate the SOC value of the power battery pack, so as to predict at any time how much energy is left in the electric vehicle energy storage battery or the SOC value of the energy storage battery, so that the battery SOC value is controlled within the working range of 30%~70%.
3. Fault diagnosis and alarm: When the battery pack power or energy is too low and needs to be charged, the alarm will be given in time to prevent the battery from over-discharging and damaging the battery life; when the battery pack temperature is too high or it is not working normally, the alarm will be given in time to ensure the normal operation of the battery.
4. Thermal balance management of battery pack: The battery thermal management system is an organic part of the battery management system. Its function is to keep the battery temperature within the normal operating temperature range through cooling systems such as fans and thermal resistor heating devices.
5. Consistency compensation: When there are differences between batteries, there are certain measures to compensate to ensure that the battery pack has stronger performance, and there are certain means to display the location of batteries with poor performance for repair and replacement. Generally, the charging compensation function is adopted. A bypass shunt circuit is designed to ensure that each cell can be fully charged, which can slow down the progress of battery aging and extend the battery life.
6. Realize communication between each detection module and the central processing unit through the bus: The difficulty and key to realizing battery management in electric vehicles lies in how to establish a more accurate mathematical model to determine the remaining energy of each battery based on the historical data of voltage, temperature and charge and discharge current of each battery collected, that is, to accurately estimate the SOC value of the electric vehicle battery.
Main Functions of an EV Power Battery Management System
Battery status monitoring: Battery status monitoring generally monitors battery voltage, current and temperature, including battery temperature, battery box temperature and ambient temperature. Battery status monitoring is the most basic function of the battery management system, and it is the premise and foundation for other functions.
Battery status analysis: Battery status analysis includes the remaining battery capacity assessment and battery aging assessment. Remaining capacity assessment is one of the most important functions in the power battery management system, and many other functions in the system rely on the results of the remaining capacity assessment. The remaining capacity is often expressed in terms of the state of charge (SOC). SOC refers to the available state of the remaining charge in the battery, generally expressed as a percentage, that is, the ratio of the remaining charge capacity in the battery to the nominal charge capacity of the battery. The degree of battery aging is also often reflected in terms of a percentage, that is, if the maximum capacity of a battery when it is “new” is 1, then after multiple cycles, the maximum capacity that the battery can load is a percentage relative to the “new” time.
Battery safety protection: Battery safety protection is the primary and most important function of the battery management system of electric vehicles. Overcurrent protection, overcharge protection, and overtemperature protection are the most common battery safety protection contents. Overcurrent protection means that if the working current exceeds the safe value during the charging and discharging process, the corresponding safety protection measures should be taken. Overcharge protection means that when the battery’s state of charge is 100%, in order to prevent damage to the battery caused by continued charging of the battery, the battery’s charging circuit is cut off. In addition, when the battery’s state of charge is 0, if the battery continues to be discharged, it will also cause damage to the battery. At this time, measures should be taken to cut off the battery’s discharge path. This is over-discharge protection. Overtemperature protection is a protective measure for the power battery when the temperature exceeds a certain limit. Overtemperature protection needs to consider the ambient temperature, the temperature of the battery pack, and the temperature of each single cell itself.
Energy management control: Energy management control includes battery charging control management, battery discharge control management and battery balancing control management. Battery charging control management refers to the real-time optimization and control of charging voltage, charging current and other parameters by the battery management system during the battery charging process. The optimization objectives include charging time, charging efficiency and charging fullness. Battery discharge control management refers to the control of the discharge current size according to the battery status during the battery discharge process. Battery balancing control management refers to taking certain measures to minimize the negative impact of battery inconsistency, so as to optimize the overall discharge efficiency of the battery pack and extend the overall life of the battery pack.
Battery information management: Battery information management includes battery information display, interaction of information inside and outside the system, and storage of battery historical information. The battery management system usually displays the battery status information through the instrument to inform the driver. The information that needs to be displayed usually includes the actual voltage, current, temperature information, battery remaining power information and alarm information. Advanced electric vehicle control is inseparable from the on-board information communication network. For the battery management system, it often has two levels of network, the intranet and the extranet. The intranet is used to transmit the internal information of the battery management system, and the extranet is used for the battery management system to interact with other components such as the vehicle controller and the motor controller. Historical information storage is not a necessary function of the battery management system, but this function is often considered in advanced power battery management systems. Historical information storage can improve the accuracy of analysis and estimation, help battery status analysis, and help fault analysis and troubleshooting.
EV Battery Management System Composition
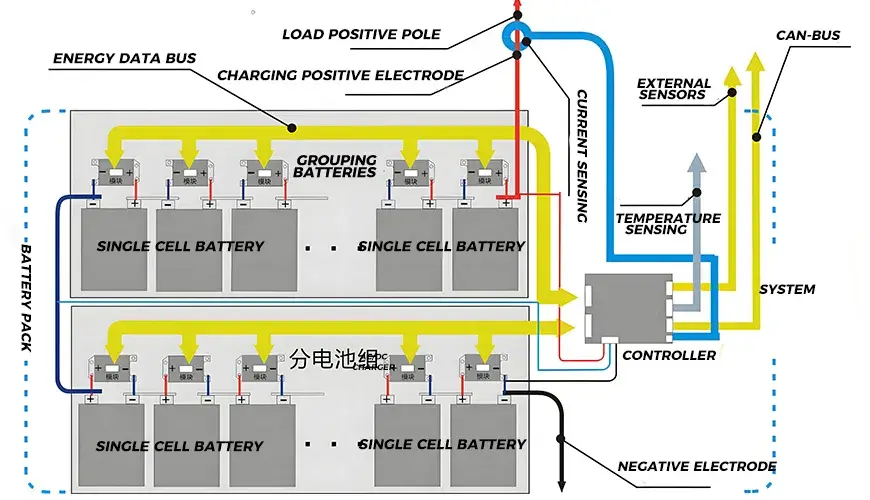
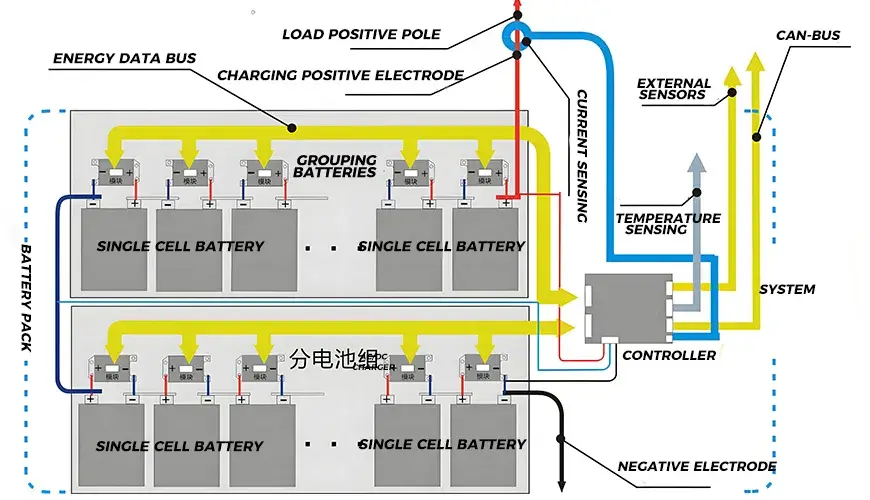
The basic components of the battery management system are shown in the figure below. It mainly consists of three parts: detection module, balanced power module and control module.
Detection module: Accurately and in real time detect the key status parameters such as voltage, current, temperature, etc. of each single cell in the battery pack, and report them to the control module through SPI.
Balanced power module: balances the voltage difference between single cells and solves the “short board effect” of the battery pack.
Control module: Completes control functions according to established strategies, realizes SOC estimation, and sends battery status data to other electronic units of the vehicle through the CAN bus.
The SOC value of the battery is obtained by integrating the current. The accuracy of the current signal detection directly affects the accuracy of the SOC value of the system. Therefore, the current conversion isolation amplifier unit is required to have higher accuracy in a larger range. Faster response speed, stronger anti-interference ability, better zero drift and temperature drift suppression ability and higher linearity.
The temperature of the battery is a key parameter to determine whether the battery can be used normally. If the temperature of the battery exceeds a certain value, it may cause irreversible damage to the battery. The temperature difference between battery packs causes imbalance between the monomers of the battery pack, which will reduce the battery life.
Voltage is an important basis for judging the quality of a battery pack. The system requires the change in the voltage value of the battery pack and the value of each battery pack at the same time, and uses algorithms to find the problematic battery pack. Therefore, the voltage sampling accuracy requirement is relatively high.
The presence of strong electromagnetic interference sources such as motors in electric vehicles places high demands on the system’s anti-interference ability, so the system is required to improve its anti-interference ability from the aspects of hardware design, printed circuit board production and software programs.
Tesla Battery Management System Introduction
One of the core technologies of Tesla electric vehicles is the battery management system. Tesla electric vehicles use Panasonic’s NCA series 18650 nickel-cobalt-aluminum-acid lithium battery series-parallel energy pack as the power source, and each Tesla Model S uses about 8,000 cells. Tesla insists on not using large-capacity battery cells because the small-capacity 18650 lithium battery technology is mature, low-cost, and safe. Once a battery cell has thermal runaway, it is not easy to affect the surrounding battery cells. However, 8,000 small battery cells are combined into a battery pack. It will greatly increase the inconsistency between battery cells, resulting in imbalance in cell temperature, charge, and voltage, causing individual batteries to be overcharged, over-discharged, and produce electrostatic reactions, thereby reducing the life and safety of the battery pack.
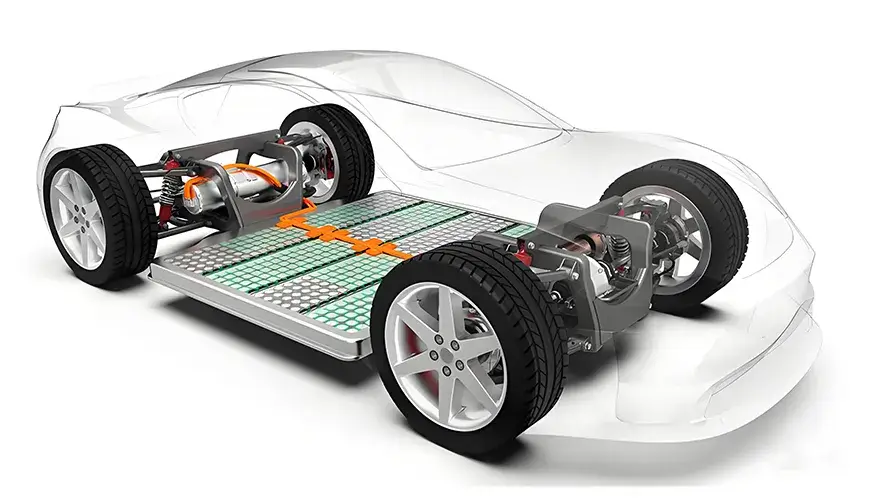
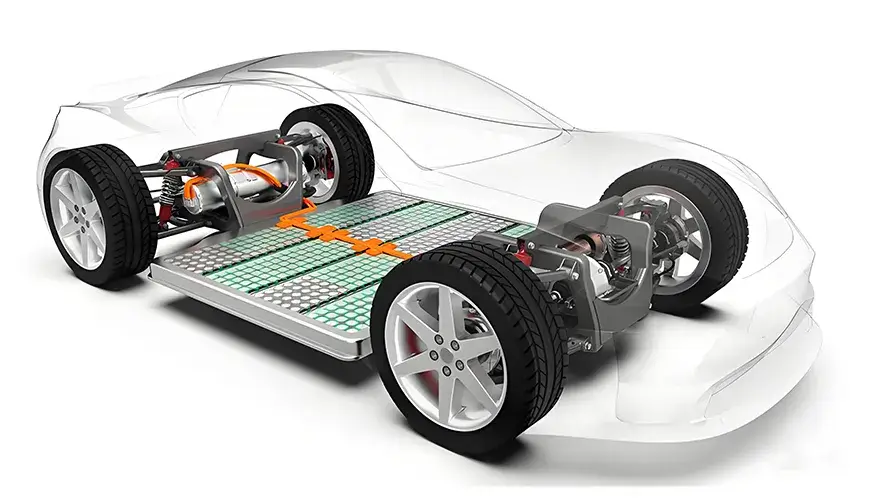
Tesla Battery Management System Features
1. Charge balancing system, effectively eliminating 18650 faulty cells: Tesla’s self-developed cell charge balancing system can effectively eliminate faulty cells and ensure the safety performance of the entire vehicle. A printed circuit board is installed at the rear of the Tesla battery pack, with many built-in power switches. One end of each power switch is connected to a 18650 battery cell, and the other end is connected to a medium-sized current collector (cell charge monitor). When a battery in the battery pack is not as charged as other batteries due to overcharging, over-discharging, or high temperature, the current collector will transfer energy between the batteries to prevent their voltage from exceeding the safe range and causing abnormal changes.
2. Battery temperature management system to improve vehicle safety performance: Tesla’s core intellectual property rights are mostly related to battery safety control systems, including battery cooling systems, safety systems, charge balancing systems, etc. The battery temperature management system also includes a battery pack temperature detection system and a battery pack liquid condensation system. Each single cell in a Tesla car battery pack is connected to a thermistor and a series of optical fibers, while the thermistor is connected to a battery monitor and the optical fiber is connected to a photosensor. When the temperature of a single cell exceeds the safety standard, the thermistor will generate an electrical signal to the battery monitor to start the battery condensation system to ensure battery safety performance. Tesla’s self-developed body liquid condensation system is a dual-mode cooling system, in which the first cooling circuit is specifically for cooling the battery pack. The battery circuit connects the battery pack to the cooling pump, the circuit is filled with coolant, and multiple cooling pipes extend to cover each single cell. The first cooling circuit connects the thermal control system, ventilation equipment and other heat dissipation devices to the battery pack thermal management system, thereby ensuring that the temperature of each single cell is below its safety value, ensuring its heat dissipation and safety performance. The second cooling circuit includes a second cooling liquid storage tank and exchanges heat with at least one rotating component, and is independent of the first cooling circuit to ensure the independence of the battery pack cooling system.
Conclusion
So, here’s how to dive into the world of electric vehicle battery management systems. This article highlights the features of EV battery management systems, and the features of Tesla’s BMS system. From ensuring safety to optimizing performance to paving the way for future innovations, the BMS is truly the unsung hero of electric vehicles. As we continue to push the boundaries of electric vehicle technology, one thing is clear: the role of the BMS will only become more critical.
The next time you hop into an electric vehicle, think about the smart system working tirelessly behind the scenes. It’s doing more than just managing the battery – it’s driving the electric vehicle revolution forward, one battery charge at a time.
Recommended reading: Electric Vehicle Charging Technology
Derek Ke
Hi, I’m Derek Ke, founder of Moreday.com, an expert in solar-protected electrical products and electric vehicle charging.
Over the past 15 years, we have helped nearly 500 customers (such as farms, residential, industrial, and commercial) in 60 countries solve new energy and green power problems. We aim to share more knowledge about solar power generation and new energy with everyone so that green electricity can enter thousands of households.